Recently viewed
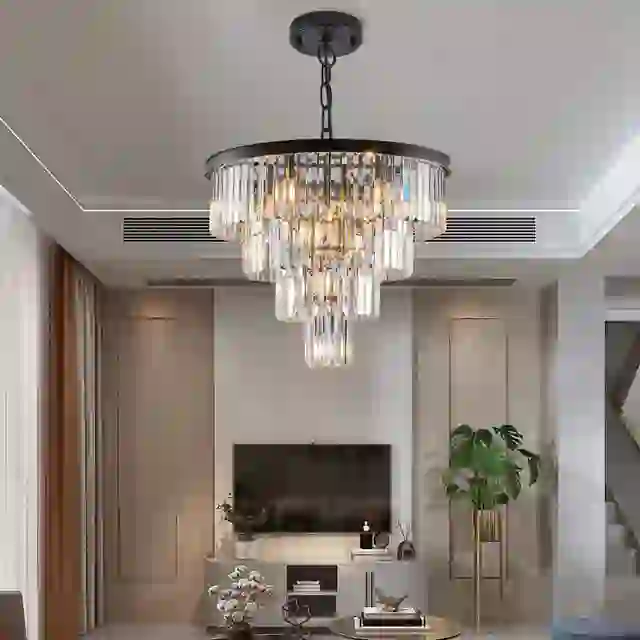
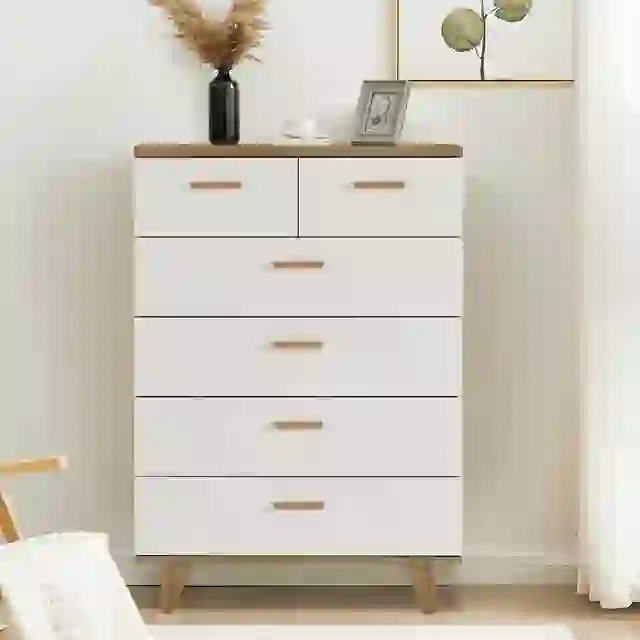
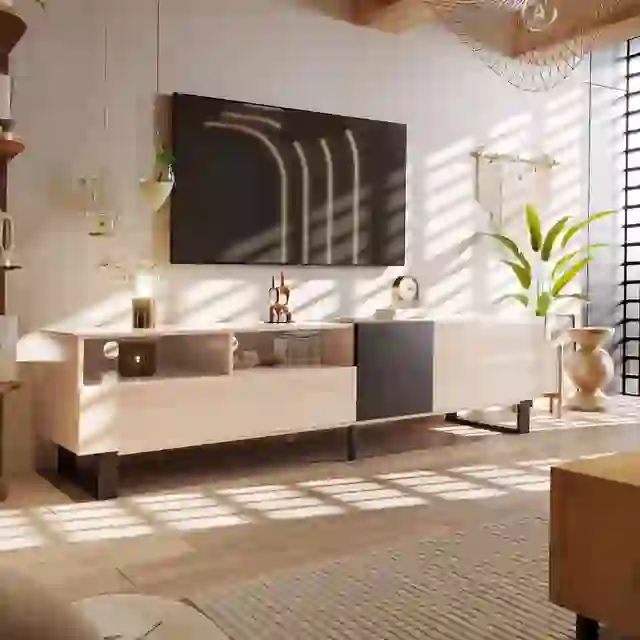

Keep buying
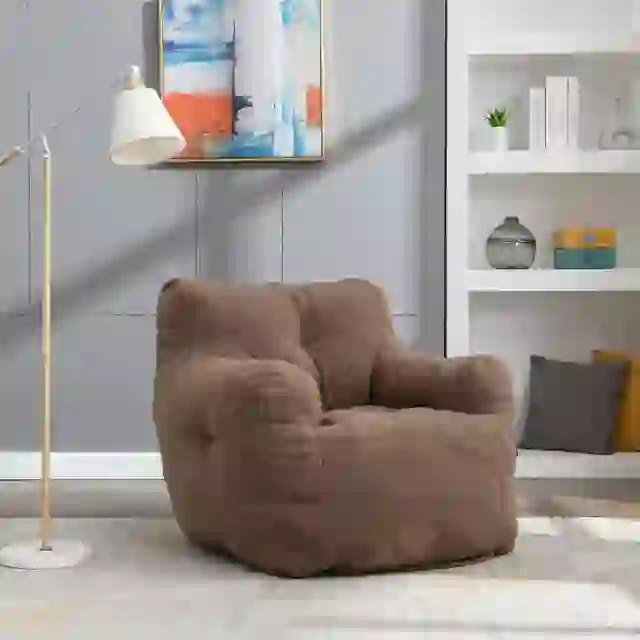
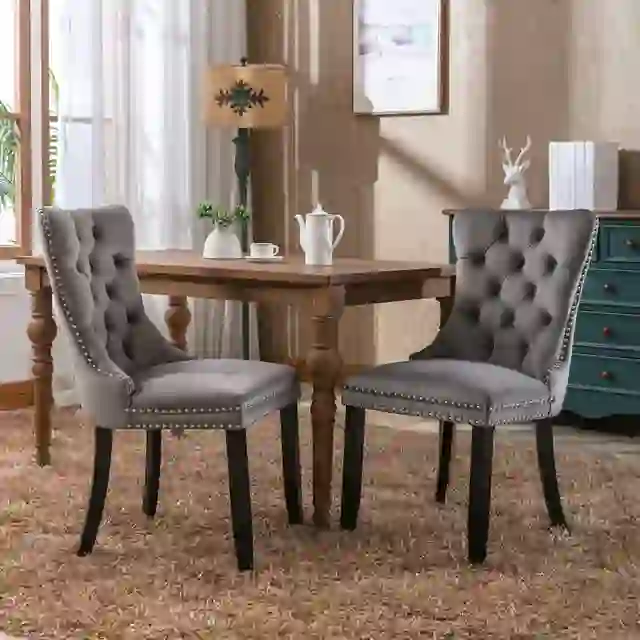
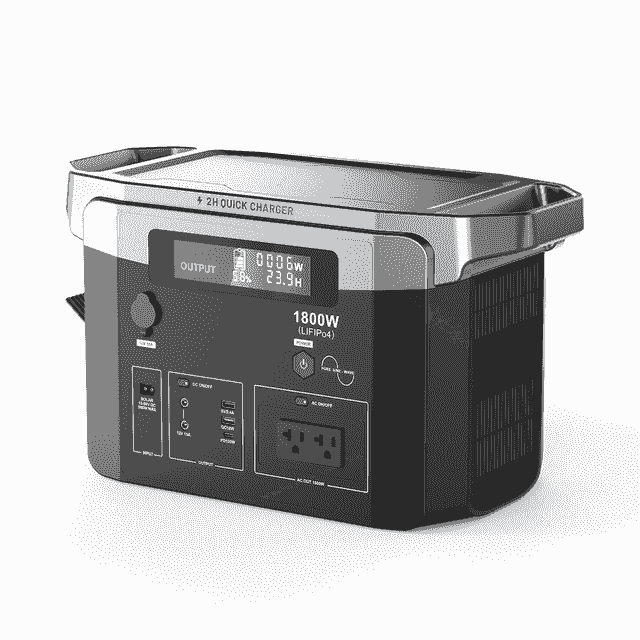
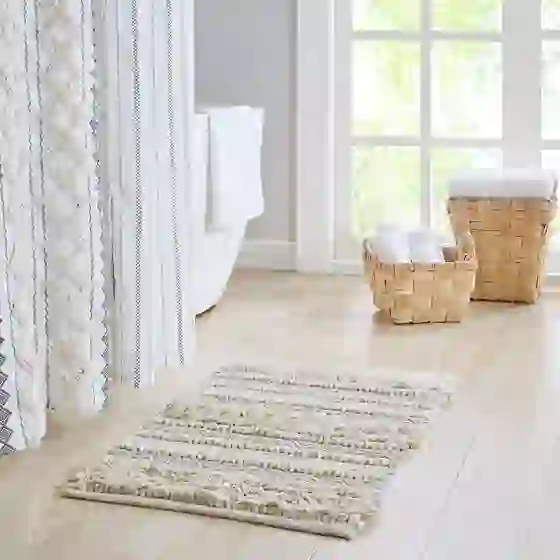
Start shopping for holiday

Sale
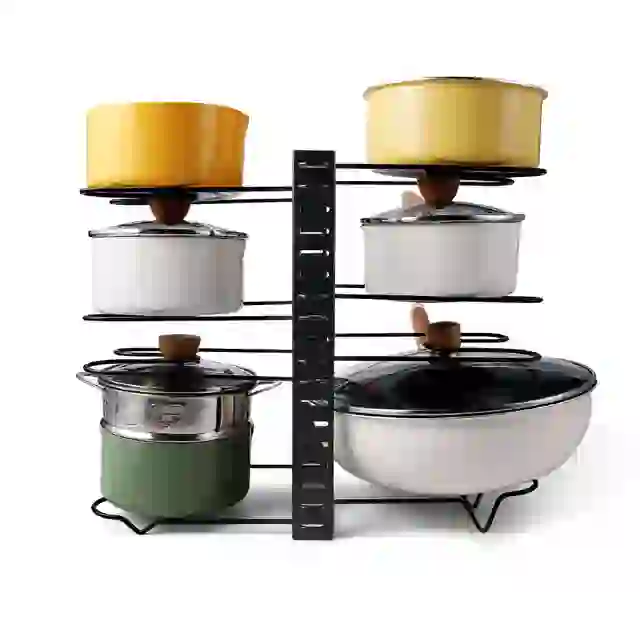
Sale
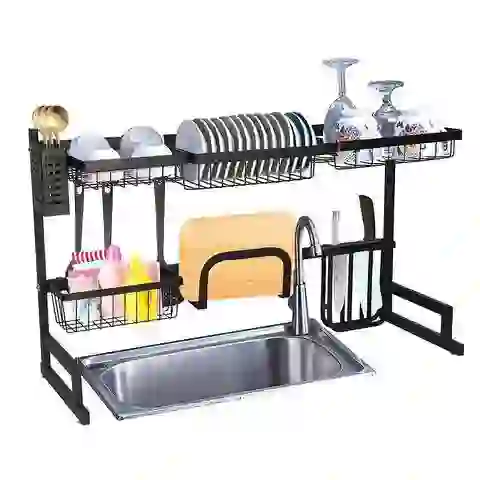
Sale
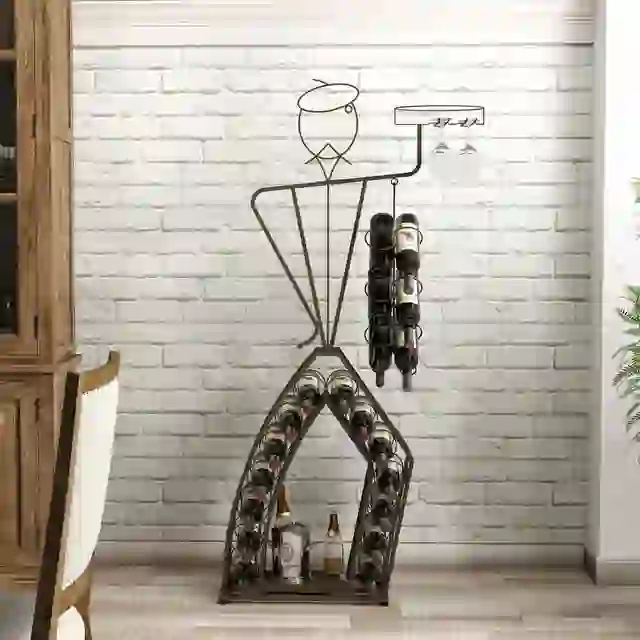
Sale
Fresh-picked favorites
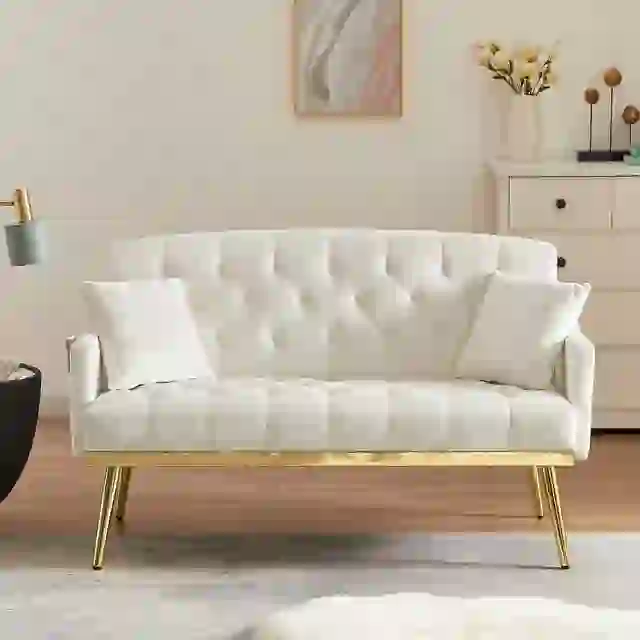
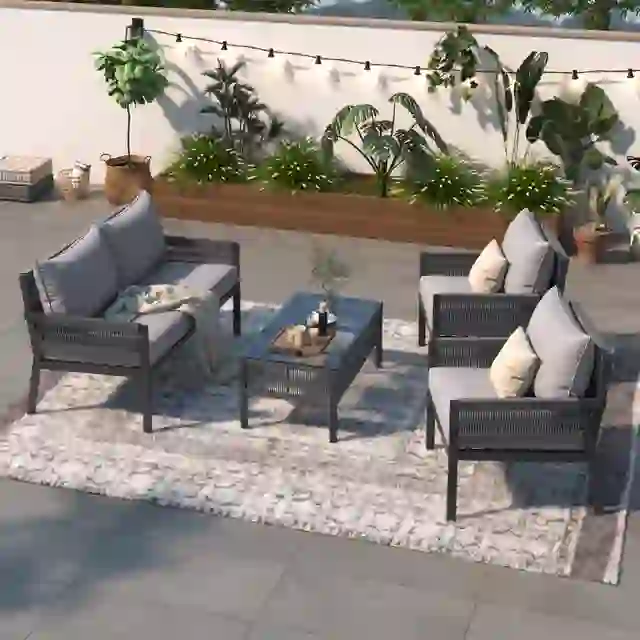
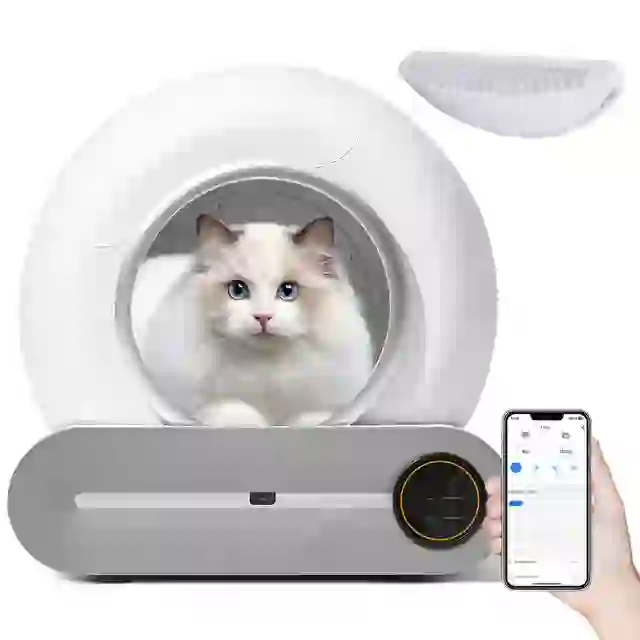
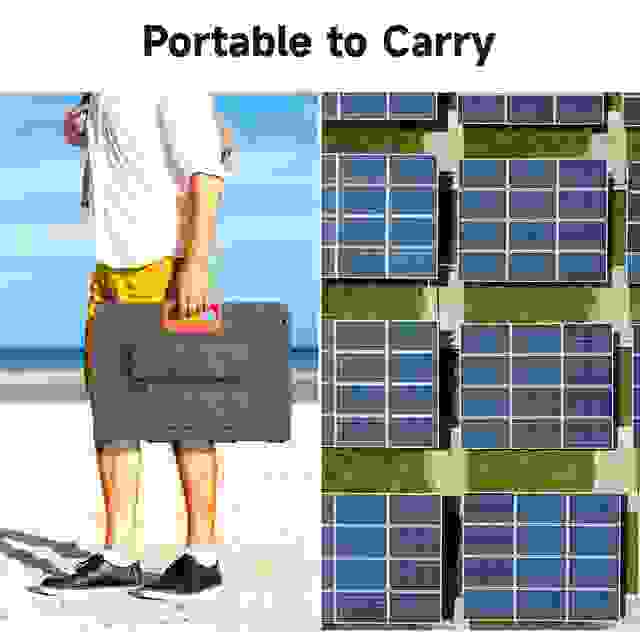
Flash sale within 24 hours
Recommend new season trends
Pick out festive gifts for everyone.
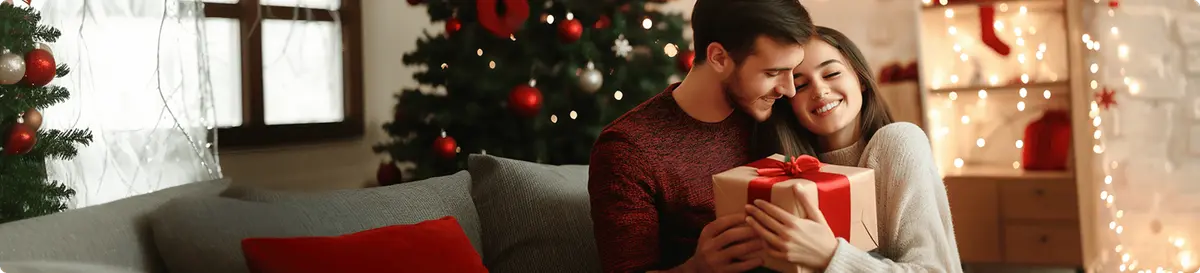
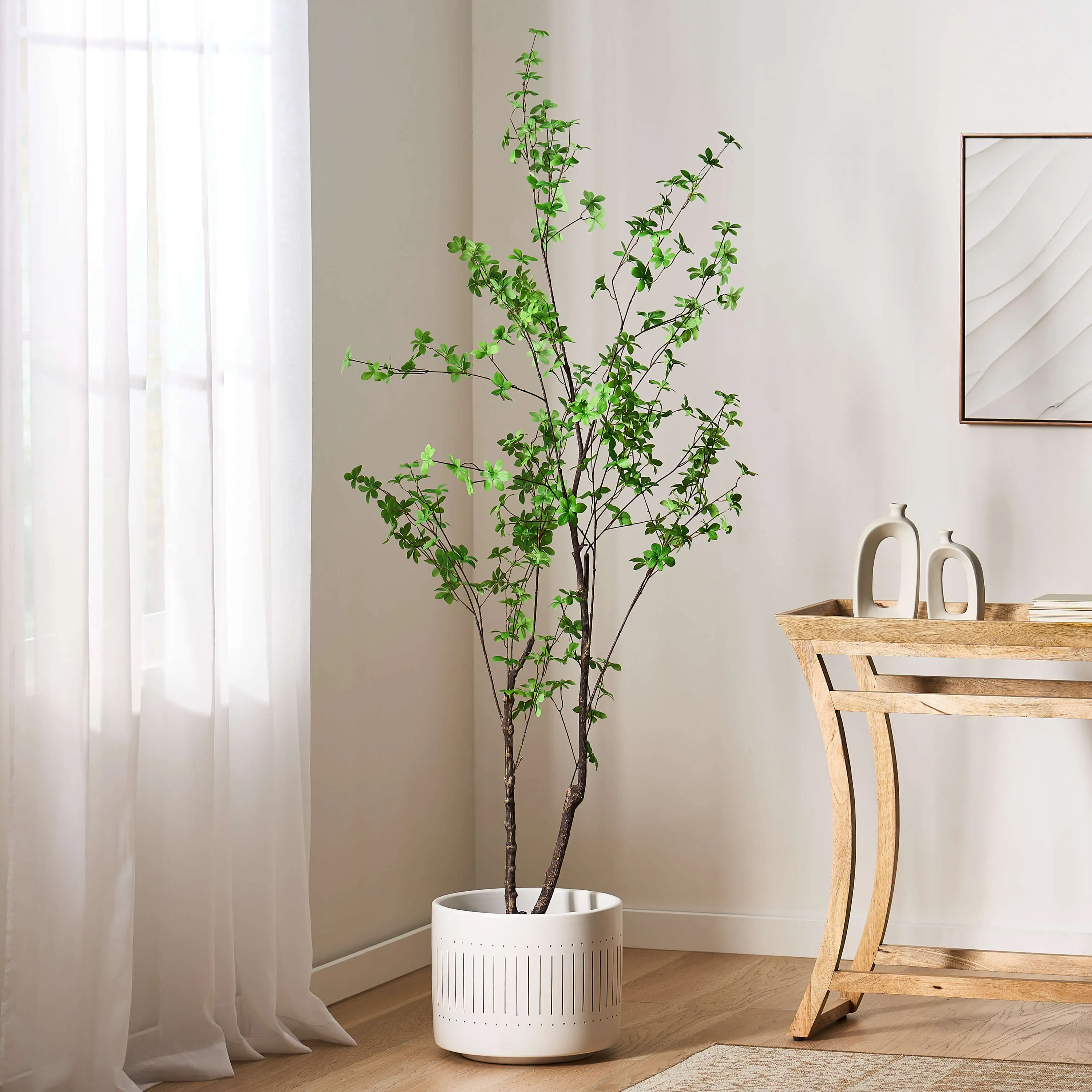
Decorate with plants and bring spring into your home
Shop nowBest sellers:home refresh
View_allShop by category
Discover all new items

Confident Choice

Anytime Customer Service

Fast & Free Shipping Over $35*

Great Deals Every Day
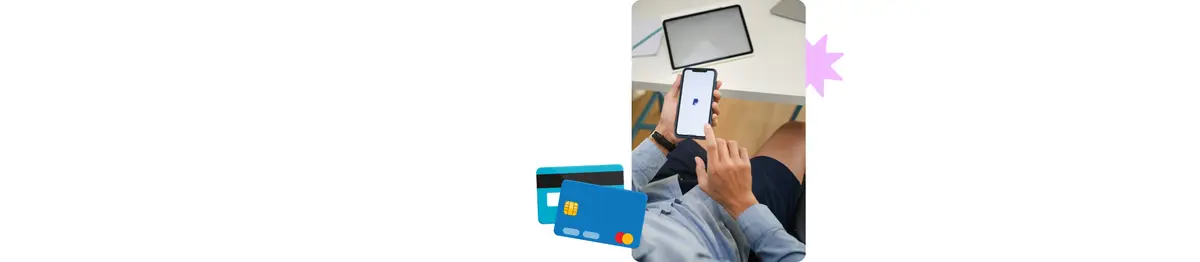
PayPal Payments, Safe and Simple
Pinshop offers you the globally trusted PayPal payment method. you can pay in just a few steps!
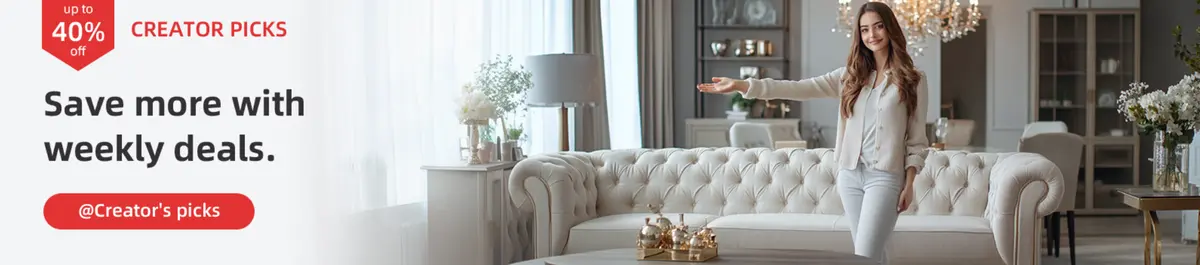